Blog
COMO TER SUCESSO NA ARMAZENAGEM LEAN
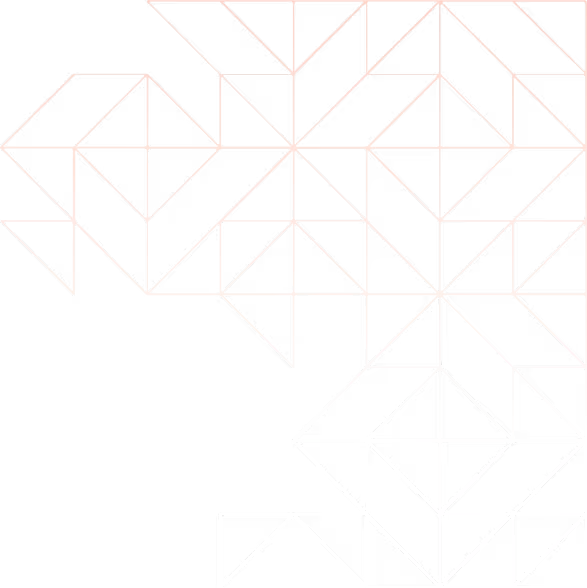
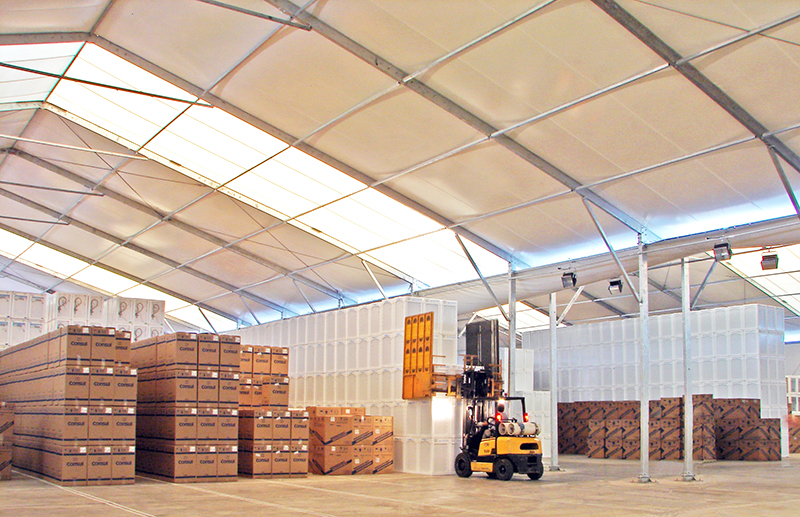
O sistema de armazenagem lean segue os princípios desse modelo de gestão, criado na década de 1950, que evita ao máximo os desperdícios a fim de aumentar a produtividade. Aqui você encontra alguns elementos considerados fundamentais para boas práticas nesse sistema de armazenagem.
A redução do tamanho dos lotes, por exemplo, entra como item crucial para a implantação desse modelo. A organização deles deve seguir a ideologia lean, que visa evitar desperdícios e aumentar a produtividade. Os produtos devem, então, estar separados por tipo, de modo que os itens mais pedidos tenham o acesso a eles facilitado – no início ou fim do corredor, por exemplo. Além disso, embalagens e rotas de separação (picking) devem ser padronizadas para cada tipo de produto, e uma etiquetagem de identificação facilita muito a organização do armazenamento.
A gestão lean repensa a forma de gerenciamento de pessoas em todos os processos de produção, e não é diferente nos armazéns. Nesse ambiente, a divisão da jornada de trabalho é padronizada e as tarefas seguem uma ideologia cíclica que uniformiza todos os os processos. As equipes são multifuncionais, para que seja possível suprir picos de demanda e eventuais faltas de funcionários. Considera-se ideal que haja remuneração por produtividade, a fim de incentivar o profissional a buscar constante aprimoramento da sua capacitação.
Em todo o processo as etapas de separação, embalagem, despacho e entrega devem estar em sincronia, reunidas em grupos de clientes (preferencialmente correlacionados), para que sejam evitadas maiores falhas durante os processos. O agendamento da chegada de caminhões, por exemplo, facilita o controle de recebimento, enquanto a limitação da demanda diária, de acordo com a capacidade máxima do centro de distribuição, controla as atividades de expedição. Para monitoramento do fluxo, a automação nos processos se torna grande aliada, e o controle humano com uso de tecnologias de comunicação à distância, garante que os funcionários verifiquem instantaneamente se os produtos tratados em cada etapa do processo estão corretos. Isso, se bem executado, evita a propagação de erros aos processos seguintes.
As rotas de entrega balanceadas também ajudam no controle do armazenamento, onde o progresso dos pedidos deve ser monitorado através de identificação – por etiquetagem, por exemplo, ou outra maneira de controle visual aparente. As eventuais irregularidades também precisam de identificação visual para que não sejam acumuladas, e devem ser escaladas em nível de prioridades a fim de eliminar a causa raiz dos problemas mais frequentes, prevenindo recorrências e promovendo melhorias nos ciclos.
Por fim, a prática mais importante que o gestor pode ter em seu lean warehousing é a boa conduta em relação a seus funcionários, e a visão sistêmica de todo o processo bem esclarecida. É importante que cada membro da equipe esteja ciente de que os processos precisam ser seguidos à risca para que nenhuma etapa seja comprometida. Sendo assim, é fundamental que o ambiente de trabalho gere um espírito de equipe. Ao final do dia, a produtividade aumentará e os desperdícios serão quase nulos se todas as etapas trabalharem em conjunto.
Posts Relacionados
Saiba mais sobre Galpão Lonado. Fale conosco para um projeto personalizado!
Seja qual for o seu setor, nossos especialistas estão à disposição para desenvolver a solução ideal para você.
Entre em contato conosco e descubra como podemos ajudar a otimizar seu espaço com eficiência e qualidade.
Solicite orçamento